6 Joseph Juran
Pareto Principle, Juran Trilogy, Quality by Design, Culture and Human Side of Quality
Rick Hardcopf; Jonathan Ebbeler; and Resa Wise
Dr. Joseph Juran (1904 – 2008)
The year 1951 marked the ratification of the 22nd Amendment to the US Constitution, color televisions first went on sale, Julius and and the first commercial supersonic flight took place. This was also the year Dr. Joseph Juran published the Quality Control Handbook. The book integrated earlier statistical pamphlets he had written and quickly became the essential reference book for quality control and management. It is the “ultimate authoritative source of answers on universal applications, procedures, techniques, and strategies for attaining superior and sustainable business results through quality.”[1]
Dr. Joseph Moses Juran was born in Braila, Romania, on December 24, 1904. Along with his family, he emigrated to the United States in 1912 to avoid oppression in Romania for the family’s Jewish faith.[2] The family settled in Minneapolis, Minnesota and Dr. Juran excelled as a student. He ultimately earned a bachelor’s degree in Electrical Engineering in 1924 from the University of Minnesota and a law degree from Loyola University in Chicago in 1935.[1]
Dr. Juran began his career with Western Electric’s Hawthorne Works. His involvement with quality management began in earnest two years later when he was one of three people assigned to a department whose purpose it was to drive statistical-based quality initiatives.[3] During this time, he developed the concept of “quality control” and was instrumental in developing quality control techniques that are widely used today. He later joined the faculty of New York University, where he taught and conducted research on quality control.
Dr. Juran’s contributions to the field of quality control are extensive. In 1937 he popularized the Pareto Principle. In 1951 he wrote the Quality Control Handbook. In 1954, he made his first visit to Japan and began a quality revolution that ultimately led to the Toyota Production System, Lean production, and Six Sigma. In 1964, he wrote the Managerial Breakthrough which described a 3-step process (the Juran Trilogy) to significantly improve product quality. In 1979 he founded the Juran Institute to continue proselytizing his quality message.[1]
Dr. Juran received many awards and honors throughout his career. He received the Brumbaugh Award in 1958, the Edwards Medal in 1962, and the American Society of Quality’s (ASQ) Grant Medal in 1967. The Brumbaugh Award is the highest honor awarded by the American Society for Quality. He was awarded the Order of the Sacred Treasure by Japan in 1981 for his long-term public service. The award is the highest attainable for a non-Japanese individual. He was also elected to the National Academy of Engineering in 1988 and U.S. President George H.W. Bush awarded him the National Medal of Technology in 1992. Dr. Juran live to 103 years old, and at age 100 he was awarded an honorary doctorate degree from Luleå University of Technology in Sweden.
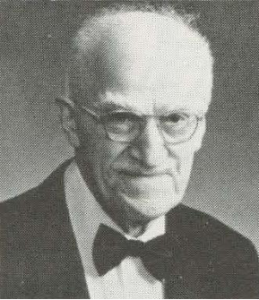
Pareto Principle
Dr. Juran was also instrumental in proselytizing the Pareto principle, which states that 80% of a company’s problems are caused by 20% of the factors that affect its quality. Said differently, a problem’s sources can be divided into two group, the ‘vital few’ (those that account for much of the problem) and the ‘trivial many’ (those which account for a relatively small portion of the entire problem).[1] Also called the 80/20 rule, the Pareto Principle is named after Italian economist Vilfredo Pareto who in 1895 noted that 20 percent of the population in Italy owned 80 percent of the wealth. It is a widely recognized quality management tool that prioritizes problems, enabling organizations to focus limit resources and time on the most impactful issues.
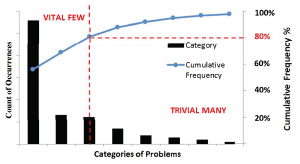
Juran Trilogy
Also known as the Juran Triad, the Juran Trilogy is a comprehensive quality management framework that focuses on meeting customer needs, continuously improving processes, and achieving business success. It has been widely adopted by organizations worldwide to help achieve and maintain high-quality standards. It consists of three interdependent components: quality planning, quality control, and quality improvement.[1]
- Quality Planning: This component involves defining the quality goals and objectives, determining the customer requirements, and creating a plan to meet these requirements. This includes identifying the critical-to-quality characteristics, designing processes to ensure that the product or service meets the customer’s needs, and creating a plan to monitor and control the processes.
- Quality Control: This component involves monitoring and controlling the processes to ensure they operate as planned. This includes inspecting and testing products and services to ensure they meet the customer’s requirements and implementing corrective actions when necessary.
- Quality Improvement: This component involves continuously improving processes to enhance customer satisfaction, reduce costs, and increase efficiency. This includes using data and feedback to identify opportunities for improvement, implementing changes to processes, and monitoring the results to ensure that the desired improvements are achieved.
By applying the principles of the Juran Trilogy, organizations can ensure that their operations are aligned with customer requirements and then continuously improve operational processes to enhance customer satisfaction, reduce costs, and achieve business success.
Quality by Design
Dr. Juran understood that the best way to improve product quality is to embed quality into the design of products and services. As such, he advocated for processes and procedures that ensured products and services were designed for manufacturability and fully met customer expectations. He codified his ideas in the book, Juran on Quality by Design.[4] Quality by Design is now widely used in manufacturing industries, such as the automobile and pharmaceutical. In fact, the FDA has a ‘Quality by Design initiate designed to maximize product efficacy and safety while enhancing manufaturability.[1]
Culture and the Human Side of Quality
Dr. Juran credits reading Margaret Mead’s Cultural Patterns and Technical Change for influencing his later work in promoting a “human side of quality”. This approach to quality management emphasized the role of top management in creating a quality culture and the importance of involving all employees in continuous improvement efforts. Dr. Juran realized early that change can only occur within the culture of an organization and change programs must be tailored to the organization’s culture and norms to be successful and sustainable. He believed that creating a quality culture required a long-term commitment and that it was necessary to educate employees about the benefits of quality and provide them with the tools and training to help them improve. Dr. Juran’s contribution to the “human side of quality” has helped organizations not only improve the quality of their products and services but create a more positive and engaged workplace culture.
The Big Ideas for Operations Management
Dr. Joseph Moses Juran was a pioneering engineer and quality management expert who made significant contributions to the field of quality control. For many, he is considered a founding father of many of the quality management programs and principles of which we are familiar today.[1] His ideas around quality, such as the Pareto Principle, the Juran Trilogy, Quality by Design, a culture of quality, and empowering employees to control and solve quality problems, are now commonplace in the current practice of operations. His ideas also helped start the quality revolution which originated in Japan in the 1970s and led to the creation of Lean Production and Six Sigma, organizational improvement methods which are commonplace in modern production and service systems. His work on quality control, quality management, and quality improvement has impacted organizations worldwide and will continue to influence how businesses operate for many years.
Sources
[1] Juran Institute, “Juran,” Juran, 2023. https://www.juran.com/about-us/dr-jurans-history/#quality-by-design (accessed Jul. 02, 2023).
[2] Toolshero, “Dr. Joseph Juran biography and theory, a quality management guru,” Toolshero. https://www.toolshero.com/toolsheroes/joseph-juran/
[3] ASQ, “Joseph Juran: A search for universal principles,” ASQ, 2023. https://asq.org/about-asq/honorary-members/juran#:~:text=Juran joined the Bell System,today as statistical quality control (accessed Aug. 02, 2023).
[4] J. M. Juran, Juran on quality by design: the new steps for planning quality into goods and services. Simon and Schuster, 1992.