11 Eliyahu Goldratt
Theory of Constraints
Jonathan Ebbeler; Rick Hardcopf; and Mike Dixon
Dr. Eliyahu (Eli) M. Goldratt (1947 – 2011)
In 1984 Dr. Eliyahu (Eli) Goldratt released his seminal book, “The Goal: A Process of Ongoing Improvement”. Goldratt’s book introduced operations mangers to the Theory of Constraints (TOC), a new way of thinking about production processes that emphasized identifying and removing bottlenecks. The book’s accessible and engaging storytelling format made it, and make it, a must-read for business leaders and managers looking to improve organizational efficiency and profitability.
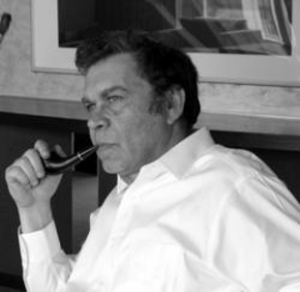
Eliyahu Moshe Goldratt was born on March 31, 1947, in Mandatory Palestine (now Israel). He was born into a rabbinic family and earned a bachelor’s degree in physics and mathematics from Tel Aviv University in 1968. He later obtained a master’s and Ph.D. in applied mathematics from Bar-Ilan University. After completing his studies, he worked briefly in academia and created a production scheduling firm called Creative Output.[1]
“The Goal” introduced readers to the concept of a bottleneck, one of the fundamental principles of TOC. Written as a fictional story about a plant manager name Alex Rogo, the easy reading style has made it a must-read for business leaders and operations managers across the world. Through a classic Hero’s Tale story, Rogo learns how to better schedule the production of his plant through understanding the importance of constrains on the overall system. Dr. Goldratt later wrote several more books, including “It’s Not Luck”, “Critical Chain”, and “Necessary But Not Sufficient”, all of which expanded on the TOC philosophy. He founded the Avraham Y. Goldratt Institute in 1986, named after his father and later called the Goldratt Group, as a consulting venture to proselytize the TOC approach worldwide. In addition to helping organizations implement TOC, Dr. Goldratt was a sought-after speaker and lecturer. He remains influential in business and management, and his ideas and teachings continue to shape how organizations approach problem-solving and performance improvement.
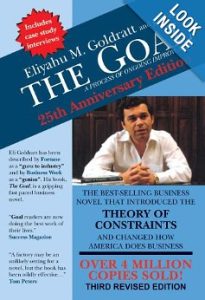
Theory of Constraints (TOC)
Goldratt developed the Theory of Constraints, a methodology for identifying and managing the constraints or bottlenecks that limit the performance of a system. TOC is based on the idea that every system has at least one constraint and that by identifying and managing that constraint, overall system capacity can be increased. The TOC approach includes five steps:
- Identify system constraint(s): Identify bottlenecks or constraints limiting system performance, such as a machine, policy, rule, or insufficient market demand.
- Decide how to exploit system constraints: Identify ways to optimize the constraint and increase its capacity to improve system capacity. This might involve adding more resources, changing work schedules, or expanding flexibility of the constraint.
- Subordinate everything else to the above decision: Managers need to align all activities and decisions within an organization to the constraint(s) identified in step 1. The goal is to ensure that all organizational activities focus on improving performance at the constraint(s).
- Elevate the system’s constraints: Engage in long-term planning to address root causes and improve output at the constraint(s). This may include upgrading technology, redesigning processes, or changing policies.
- Continuously improve the system: Continuously improve by identifying new constraints and returning to step 1.
TOC emphasizes flow as a measure of system performance, rather than efficiency and cost reduction.[2]
Drum-Buffer-Rope (DBR)
Drum-Buffer-Rope is the TOC scheduling process. The main points of DBR include:
- The Drum: The “Drum” represents the production pace set by the constraint or bottleneck in the system. The production rate is based on the constraint’s capacity and the demand for the product. The constraint is the limiting factor in the system and it determines the maximum rate of production for the system.
- The Buffer: The “Buffer” is a stockpile of inventory maintained in front of the constraint to protect it from any variability in the system. The buffer is typically made up of finished goods, work-in-progress inventory, or time.
- The Rope: The “Rope” is a signaling mechanism that controls the release of materials to the system. The Rope ensures that materials are released into the system in a controlled manner based on the production rate set by the Drum.
- Prioritization: DBR prioritizes production based on the constraint and schedules production to ensure that the constraint is always working at full capacity. It aims to minimize the time that non-constrained activities wait for resources, which helps to improve overall system efficiency.
- Continuous Improvement: DBR also emphasizes the importance of continuous improvement and optimization of the production process. This involves avoiding constraint downtime and looking for ways to improve output at the constraint, thereby increasing system capacity.
DBR synchronizes the production process by creating a buffer (a stockpile of inventory) before the drum (bottleneck or constraint) and using a rope (a signaling mechanism) to control the release of materials into the system. The key idea is to ensure the production system operates at a pace set by the constraint, while continuously improving system capacity by increasing capacity at the constraint.[3]
Critical Chain Project Management (CCPM)
Critical Chain Project Management used TOC concepts to reduce project lead time and improve on-time project performance.[4] The main elements of CCPM include:
- Identify the Critical Chain: CCPM begins with identifying the longest chain of dependent tasks in a project, known as the “critical chain” or “critical path”. The critical chain includes project tasks and any resource dependencies that may impact the project’s completion time.
- Buffer Management: Once the critical chain is identified, the critical path is ‘buffered’ to ensure the project stays on track. Buffering involves creating a “project buffer” at the end of the critical chain to protect it from delays and “feeding buffers” at each resource constraint to ensure that critical resources are available when needed.
- Resource Optimization: CCPM also considers the availability of critical resources, i.e., those that support critical chain activities. CCPM ensures resources are available for critical chain activities, thereby avoiding project delays and inefficiency.
- Multitasking Reduction: CCPM emphasizes the importance of reducing multitasking, which can significantly cause delays and inefficiencies in project management. CCPM encourages teams to focus on completing one task at a time rather than juggling multiple tasks simultaneously.
- Agile Mindset: CCPM encourages an agile mindset, which means that teams should be open to change and willing to adjust the project plan as needed. CCPM also emphasizes the importance of communication and collaboration between team members to ensure everyone is aligned and working towards the same goals.
Throughput Accounting
Throughput Accounting is a method of accounting that uses TOC concepts to improve organizational decision making and profitability.[5] It focuses on maximizing system throughput rather than just reducing costs. The key accounting elements in Throughput Accounting include:
- Throughput (T): The rate at which the system generates money through sales. TOC emphasizes increasing throughput as the most critical measure of performance.
- Inventory (I): The amount of money the system has invested in purchasing things it intends to sell. Inventory ties up cash, and the goal of TOC is to minimize inventory while ensuring there is enough to meet demand.
- Operating expenses (OE): All the costs incurred by the system to turn inventory into throughput. TOC aims to reduce operating expenses while maintaining the quality of the product or service.
The goal of Throughput Accounting is to increase system throughput, while simultaneously reducing inventory and operating expenses. It provides a more accurate way of measuring a system’s financial performance by looking at how an organization generates cash, how much money is tied up in inventory, and how much it costs to produce and deliver a product or service.
The Big Ideas for Operations Management
Dr. Eli Goldratt’s innovative ideas have profoundly impacted how organizations approach process improvement. His ideas are as relevant and popular today as they were when they were first developed. His most prominent contributions include:
- Theory of Constraints (TOC): System capacity can be increased by identifying constraints, maximizing output at the constraint, and continuously increasing constraint capacity.
- Drum-Buffer-Rope (DBR): An optimal production schedule is created by identifying the constraint (the ‘drum’), adding inventory in front of constraint to ensure it is not starved by system variability (buffer), and using a signaling mechanism (rope) to release work into the system based on the production rate at the constraint (drum).
- Critical Chain Project Management (CCPM): Projects can be completed faster and more reliably by identifying and buffering the critical path, ensuring resource availability for critical path activities, reducing multitasking, and adjusting project plans when needed.
- Throughput Accounting: A TOC method of accounting that helps organizations improve profitability by increasing the ‘throughput’ of the system (roughly contribution margin generated by a sale), reducing inventory, and managing how much it costs to produce and deliver a product or service (operating expenses).
Sources
[1] GMG, “Biography of Eli Goldratt,” Goldratt Marketing Group, 2022. https://www.toc-goldratt.com/en/biography-of-eli-goldratt
[2] Lean Production, “Theory of Constraints (TOC),” Lean Production, 2022. https://www.leanproduction.com/theory-of-constraints/
[3] C. Roser, “A Critical Look at Goldratt’s Drum-Buffer-Rope Method,” Allaboutlean.com, 2022. https://www.allaboutlean.com/drum-buffer-rope/
[4] S. Laoyan, “The basics of critical chain project management,” Asana, 2022. https://asana.com/resources/critical-chain-project-management
[5] SOB, “Throughput Accounting,” Science of Business, 2022. https://www.scienceofbusiness.com/throughput-accounting/