7 Philip Crosby
Quality is Free, Zero Defects, Doing it Right the First Time
Jonathan Ebbeler and Rick Hardcopf
Philip Crosby (1926 – 2001)
Philip Bayard Crosby was born on June 18, 1926 in Wheeling, West Virginia. He is best known for his hugely popular book, “Quality is Free”, which was first published in 1979. In that book and others he authored, Crosby popularized quality ideas that became synonymous with his name, including “quality is free”, “zero defects”, and “do it right the first time”. While his quality ideas were not necessarily new, as they built upon the ideas of other quality thinkers, like Edwards Deming and Joseph Juran, he had the ability to speak the language of business executives, i.e., profit. As such, his views on quality inspired hundreds of companies around the world to improve their quality and save money in the process. He was passionate about his work and continued sharing his knowledge until his death in 2001.
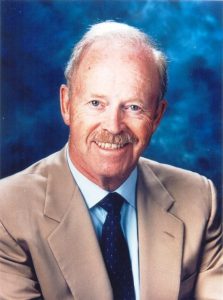
Mr. Crosby served in the Navy during World War II and then again in the Korean War. In between wartimes, he graduated with a degree from the Ohio College of Podiatric Medicine. Despite a medical degree, Crosby spent most of his career working in manufacturing organizations, and later, as a management consultant. In 1952 he started as an assembly line worker at Crosley Corporation in Richmond, Indiana. It was here that Crosby was first introduced to the world of quality. In 1957, Crosby became a quality control manager for the Martin Corporation, marking his first official role in quality. In this role, he developed his ideas for zero defects, which would later become a critical principle in his theories and writings about quality improvement. His final corporate role was as Director of Quality and Vice President of the ITT company from 1965-1979.
In 1979, Crosby founded Phillip Crosby Associates (PCA) in Winter Park, Florida, leaving behind his corporate job. Within the same year, Crosby’s first book, Quality is Free, was released. Over his lifetime, Crosby would author fourteen books. His consulting firms taught managers how to create a culture of mistake prevention and ‘doing things right the first time’. He was a popular speaker and firms from all around the world invited Crosby to teach quality management principles to their organizations.
Crosby’s Quality Principles
It was common practice in the 1950s and 60s for manufacturers to set defect tolerances and then try to produce products at or below target defect levels. Quality ‘assurance’ meant checking for defects at the end of the production line, before finished products were shipped to customers. In contrast, Crosby advocated a ‘zero defects’ mindset, i.e., businesses should strive to make perfect products with no defects. This did not mean that human mistakes do not happen – they do; however, managers should not start the day with an acceptable allowance for mistakes or sub-standard products. Critical to his thinking was the need for quality ‘control’. In contrast to quality assurance, quality control means continuously monitoring processes for mistakes and then correcting mistakes in the process ‘before’ they cause product defects. In Crosby’s thinking, expecting to fail, even a little, is a loss for the company. Companies should instead work to continuously improve processes, thereby reducing defective products to zero.
Crosby’s quality control system requires a culture of prevention, i.e., preventing mistakes before they happen. This requires continuous process review and improvement, and continuous process improvement should be visible. This mindset starts at the top and weaves its way into every level of an organization. Crosby’s view of quality requires the effort of all employees. To that end, employees should be trained in how to improve quality. Crosby taught that there is a cost to nonconformance and poor quality. The ‘cost of poor quality’ is the cost of not doing something right the first time, thus having to rework or remake products. He espoused that it costs significantly less to spend time and effort eliminating process mistakes than to rework or scrap defective products. Crosby estimated that allowing things to go wrong (and subsequently having to fix them) could cost organization 20-25 percent of revenue.
Quality improvement thus equates to profit improvement.
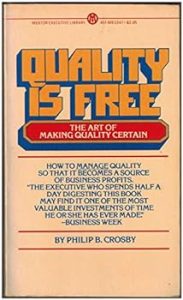
The Big Ideas for Operations Management
Philip Crosby advanced key concepts initially proposed by prior quality gurus, including defect prevention, continuous improvement and the pursuit of perfection, and worker empowerment. His popular slogans, including “quality is free”, “zero defects”, and “do it right the first time”, among others, were easy for executives and managers to understand. They explained how quality improvement, previously perceived to be an organizational expense, could instead drive significant profit. In capturing the attention of business executives, the concepts became central to production systems around the world.
”The Quality Man” Philip Crosby Explains Absolutes of Quality Management
References
British Library. (2023). Philip Crosby. British Library. https://www.bl.uk/people/philip-crosby
History-biography. (2023). Philip Crosby Biography. History-Biography. https://history-biography.com/philip-b-crosby/
Quality Gurus. (2023). Philip Crosby: The Mans Who Said “Quality is Free.” Quality Gurus. https://www.qualitygurus.com/philip-crosby/