6 Edwards Deming
TQM, ‘Fix the Process, Not the People’, Deming Wheel (PDCA), 14 Points for Management, 7 Deadly Management ‘Diseases’
Jonathan Ebbeler; Resa Wise; and Mike Dixon
Dr. W. Edwards Deming (1900 – 1993)
The year 1982 marked several milestones, including the release of Michael Jackson’s Thriller, the beginning of the breakup of AT&T, the start of the Falklands War between Argentina and Britain, the release of Stephen Spielberg’s E.T., the introduction of the Compact Disc (CD), the introduction of the Commodore 64 (the best-selling personal computer of all time), and the release of Dr. W. Edwards Deming seminal book, “Out of the Crisis”. Dr. Deming’s book helped shape the field of quality management and set the stage for the Total Quality Management (TQM) movement. The book’s ideas and methods, including the introduction of ‘14 Points for Management’ and the ‘Seven Deadly Diseases of Management’, continue to be widely used and highly influential to today’s operations management professionals.
Dr. W. Edwards Deming was an American statistician, engineer, and management consultant best known for his work in the field of quality control and continuous improvement. He was born in Sioux City, Iowa in 1900. He received a BS in electrical engineering from the University of Wyoming in 1921, an MS from the University of Colorado in 1925, and his Ph.D. in mathematical physics from Yale University in 1928. [1]
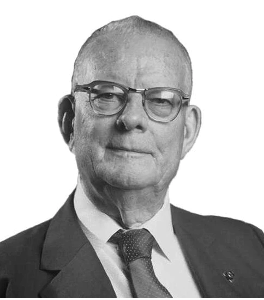
Globalization of Dr. Deming’s revolutionary quality improvement ideas began in the 1940s when he was invited to consult for the Japanese government after World War II. He spent the next several decades working in Japan, teaching Japanese manufacturers the principles of quality control and continuous improvement. He became a popular figure in Japan and along with Professor Joseph Juran, was widely credited with playing a significant role in Japan’s post-WWII economic recovery. His tremendous success in Japan led the Japanese Union of Scientists and Engineers (JUSE) to create the prestigious “Deming Prize” in 1951. It was originally awarded only to Japanese companies that demonstrated excellence in quality improvement. However, it was later made available to companies from around the world.
Dr. Deming’s success in Japan eventually brought him to the attention of American businesses and he became a sought-after consultant in the United States. He is known for his 14 points for management, emphasizing the importance of continuous improvement, leadership, and management’s role in creating a quality culture. Throughout his career, Dr. Deming was a passionate advocate of quality control and continuous improvement principles. He was a prolific author and speaker, and his books, including “Out of the Crisis” and “The New Economics for Industry, Government, Education,” became formative works in the field of Total Quality Management (TQM).
Dr. Deming was widely recognized for his contributions to the field of quality control and was awarded numerous honors, including the National Medal of Technology in 1987. That same year, the US version of the Deming Prize was established, the Malcolm Baldridge National Quality Award. He passed away in 1993, but his legacy lives on and his teachings continue to influence the management practices of businesses and organizations worldwide.
Deming’s 14 Points
Dr. Deming developed 14 points for management to improve organizational quality and productivity.
- Create constancy of purpose towards improvement of product and service.
- Adopt the new philosophy.
- Cease dependence on inspection to achieve quality.
- End the practice of awarding business on price tag alone.
- Improve constantly and forever the system of production and service.
- Institute training on the job.
- Institute leadership.
- Drive out fear.
- Break down barriers between staff areas.
- Eliminate slogans, exhortations, and targets for the workforce.
- Eliminate work standards that prescribe numerical quotas.
- Remove barriers that rob people of pride in workmanship.
- Institute a vigorous program of education and self-improvement for everyone.
- Take action to accomplish the transformation.
The points provide a roadmap for organizations to create a culture of continuous improvement. They move away from a focus on inspection and blaming workers, and instead focus on improving processes and empowering employees. [2]
7 Deadly Diseases
Dr. Deming also identified seven ‘deadly diseases’ of management (in the U.S.), which he saw as obstacles to achieving organizational quality and productivity. They are:
- Lack of constancy of purpose.
- Emphasis on short-term profits and short-term strategy.
- Evaluation of performance, merit ratings, and annual performance reviews.
- Mobility of management and job hopping.
- Running a company on visible figures alone.
- Excessive medical costs.
- Excessive costs of liability, fueled by lawyers who work for contingency fees.
The ‘deadly diseases’ reflect standard management practices and attitudes that Deming believed were detrimental to organizational success. By avoiding the diseases, he believed organizations would create a culture of continuous improvement and foster a more productive and efficient work environment. [3]
Process Not People
Dr. Deming’s “process, not people” idea for quality management and continuous improvement is based on his belief that processes drive business outcomes, not individuals alone. He felt that organizations often blamed employees for poor quality or inefficiencies when the real root causes are the processes and systems. Thus, when trying to improve quality and productivity in an organization, the focus should be on improving processes, not trying to ‘fix’ the employees. By improving processes, organizations can improve the performance of all employees and create a more productive and efficient workplace. The ‘process, not people’ principle is central to Dr. Deming’s quality improvement philosophy and is a crucial component of the PDCA cycle, which he popularized as a tool for continuous improvement.
PDCA Cycle (Deming Wheel)
Dr. Deming popularized a continuous improvement model called the Plan-Do-Check-Act (PDCA) cycle. Originally developed by Walter Shewhart and also known as the Shewhart Cycle, Deming Cycle, or Deming Wheel, the PDCA cycle is a method to continuously identify, evaluate, and solve organizational problems and process issues in a systematic and data-driven manner.
The four steps of the PDCA cycle are:
- Plan: Identify the problem or opportunity for improvement, set goals, and develop a plan to address the issue.
- Do: Implement the plan, collect data, and observe the results.
- Check: Analyze the data and compare it to the goals set in the planning phase.
- Act: Based on the analysis results, make changes to the plan and process, and then repeat the cycle.
The PDCA cycle is rooted in statistical process control methodology developed by Walter Shewhart. Deming built upon Shewhart’s ideas and introduced the concept of the PDCA cycle to a broader audience. He emphasized the importance of using data and statistical analysis to drive improvement and to make informed decisions. By combining Shewhart’s ideas about statistical process control with his own ideas about continuous improvement, Dr. Deming helped popularize the PDCA cycle as a tool for organizations to continuously improve quality, reduce waste and inefficiency, and increase productivity.
The PDCA cycle has had a significant impact on the way modern organizations approach quality management and continuous improvement. It provides a structured approach for problem-solving and improvement. At the same time, the focus on data-driven decision-making and statistical process control helps ensure that improvements are based on evidence and sustainable. In fact, the roots of the hugely popular Six Sigma DMAIC (Define-Measure-Analyze-Improve-Control) process improvement methodology come from PDCA [4].
The Big Ideas for Operations Management
Dr. W. Edwards Deming was a visionary in the field of quality control and continuous improvement. His ideas and teachings profoundly impacted the field of operations management. His work remains highly relevant today as organizations continue to seek ways to improve processes and increase efficiency [5]. His most prominent ideas for operations management include:
- Continuous Improvement: Dr. Deming believed that organizations should adopt a continuous improvement approach, focusing on making incremental improvements to processes over time.
- PDCA Cycle: Dr. Deming popularized the Plan-Do-Check-Act (PDCA) cycle, which is a continuous improvement model that helps organizations identify and solve problems in a systematic and data-driven manner.
- Statistical Process Control: Dr. Deming believed that understanding the variability in processes was the key to improving them. He strongly encouraged the use of statistical process control methods, such as control charts, to monitor and improve processes.
- Focus on Process, Not People: Dr. Deming’s principle of “process, not people” means improving processes by focusing improvements on the process itself (make the process ‘mistake proof’), rather trying to ‘fix’ the people working in the process.
- Employee Empowerment: Dr. Deming believed that employees should be empowered to continuously improve processes and that organizations should foster a culture of continuous improvement that values all employees’ contributions.
- Total Quality Management: Dr. Deming’s philosophy of continuous improvement and his emphasis on data-driven decision-making helped to lay the foundation for the Total Quality Management (TQM) movement. TQM, as a precursor to Six Sigma, is a holistic approach to improve quality that involves all employees and all aspects of an organization.
Sources
[1] British Library, “W Edwards Deming,” British Library, 2022. https://www.bl.uk/people/w-edwards-deming
[2] ASQ, “W. Edwards Deming’s 14 Points for Total Quality Management,” American Society for Quality, 2022. https://asq.org/quality-resources/total-quality-management/deming-points
[3] T. Hessing, “W. Edwards Deming,” SixSigmaStudyGuide.com, 2022. https://sixsigmastudyguide.com/william-edwards-deming/
[4] J. Roussel, “Common Questions about the DMAIC Cycle for Improvement,” KaiNexus, 2021. https://blog.kainexus.com/improvement-disciplines/six-sigma/common-questions-about-the-dmaic-improvement-cycle#:~:text=The roots of DMAIC come,Bell Laboratories during the 1930s.
[5] Deming Institute, “Deming the Man,” The Deming Institute, 2022. https://deming.org/deming-the-man/