11 Shigeo Shingo
Seek perfection (Zero-defects), Pokayoke, SMED, One-piece flow, the Shingo Prize
Ken Snyder and Rick Hardcopf
Shigeo Shingo (1909-1990)
Shigeo Shingo was a Japanese industrial engineer who played a key role in assisting Toyota develop the Toyota Production System (TPS), a precursor to the highly popular Lean production system popular around the world today. He created several techniques which are foundational to Lean production, including pokayoke (error-proofing), single-minute exchange of die (SMED), and one-piece flow. He was also relentless in advocating for ‘zero defects’, a culture of continuous improvement and relentless pursuit of error-free production. He authored 17 books, seven of which were translated into English.[1] His ideas were heavily influenced by leading productivity thinkers of the era, including Frank and Lillian Gilbreth, Frederick Taylor, Dr. Joseph Juran, and W. Edwards Deming.
Shigeo Shingo was born on January 8th, 1909 in the city of Saga on the Japanese island of Kyushu. His college years were spent learning about Frederick Taylor and other operations management pioneers. He graduated from the Yamanashi Technical College in 1930 with a degree in Industrial Engineering and subsequently began working at the Taipei Railway Factory. It was there he began perfecting the production flow methods that defined his life and created his legacy. In 1943, during WWII, he was sent by the Ministry of Munitions to the Amano manufacturing plant in Yokohama. Using his production flow improvement ideas, he was able to double the plant’s productivity. Between the mid-1940’s and mid-1950’s, Shingo continued to perfect his ideas around production flow and process efficiency.[2]
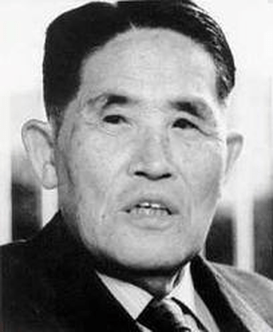
Work with Toyota
While working with the Japan Management Association (JMA) in 1955, Shingo received an invitation from Taiichi Ohno, considered the Father of TPS, to visit and work with Toyota. That introduction led to lengthy partnership until 1982 (about 27 years). At Toyota, he taught quarterly week-long workshops known as P-Courses (for “P” for productivity), ultimately training over 3,000 Toyota leaders. He gave course participants a business card/photo of himself pointing to his head with a caption that read,
“Shingo Sensei says: Kaizen is more about using your head than it is about spending money.” [2]
He also worked with Toyota on various projects. For example, he helped Toyota reduce die changeovers from 2-4 hours to under 10 minutes and made improvements to Toyota’s just-in-time (JIT) system. Shingo wrote one of the seminal books about TPS that helped introduce the system to the rest of the world.[3]
Seek Perfection
At the core of Shingo’s thinking around process flow improvement was the endless pursuit of waste and the concept of ‘perfect production’. Waste included anything that did not deliver value to the customer such as defects, lost production time due to product changeovers, and inventory of any type. Inventory was especially ‘evil’ because it stops flow and thus value creation, and because it hides quality and productivity problems. It was this endless pursuit of perfection that ultimately led Shingo to the tools and ideas for which he is prominently known, including pokayoke, single-minute-exchange-of-dies (SMED), and one-piece flow.
Pokayoke (Error-Proofing)
Even though the statistical quality control (SQC) movement was sweeping Japan after World War II, and Shingo was a big fan of Deming and SQC, Shingo ultimately realized that ‘perfect production’ required a different approach to improving quality, i.e., it required eliminating defects from occurring, not measuring and controlling them after they occurred. His statement, “Don’t measure defects – eliminate them!” reflects this revolutionary approach. This led to the concept of ‘perfectly’ eliminating problems through error prevention (zero defects). For example, he argued that work stoppages due to equipment breakdowns could be prevented by routinely conducting preventive maintenance on production equipment. He also argued that safety incidents could be completely eliminated by identifying and eliminating the underlying safety issues. Ultimately, the pursuit of error-free production led to, in partnership with Toyota, the development of pokayoke. Pokayoke methods prevent errors from occurring and if they do occur, prevent them from being passed to the next operation. By using pokayoke, as implemented by production workers (quality at the source), Shingo demonstrates in his book ‘Zero Quality Control’ how to achieve the perfect elimination of defects. As he added to the cover of the book, “Defects = ø is absolutely possible!”.[4]
Single-Minute Change of Dies (SMED or Quick Changeover)
To eliminate lost production time due to product changeovers, Shingo developed the Single-Minute Exchange of Dies (SMED) method. More than any other concept, the SMED method brought him worldwide acclaim. It led to numerous academic articles and many consulting contracts. However, rather than basking in the attention, Shingo argued that SMED was not enough. Even very fast changeovers still caused delays and led to increased work-in-process inventory. Shingo argued that “The best changeover is no changeover at all.”
One-Piece Flow (or as Shingo called it, “Non-stock Production”)
To eliminate product changeovers altogether, and the associated inventory, Shingo developed the idea of single-piece flow or ‘non-stock production’. As he describes it, “In the non-stock production system, inventory is considered an absolute evil that must be absolutely eliminated.”[4] He describes the system as processing one-piece at a time so that there is no inventory. While the ‘non-stock production’ terminology did not survive, the concept of “one-piece flow” did survive and gradually became one of the key principles of Lean production. As a note, Shingo was a strong advocate of Toyota’s ‘Just-in-time’ (JIT) production system. JIT ensures that the ‘right part is at the right place at the right time’. JIT is one pillar of TPS and Lean production. Much of Shingo’s consulting work at Toyota involved helping clients make improvements to achieve JIT. However, Shingo was not a proponent of Kanban, the highly popular inventory management system used in JIT production, because it unnecessarily locked in inventory. He developed the ‘non-stock’ production system to combat inventory associated with the Kanban system.
The Shingo Prize and the Shingo Institute [5]
In 1988, Shingo was invited to speak at an operational excellence conference at Utah State University. While there, he was awarded an honorary doctorate and requested by the university to use his name to start a prize to recognize great achievements in organizational and operational excellence. With his permission, the Shingo Prize was launched, with recipients in over 30 countries and from every type of organization – including hospitals, banks, insurance companies, logistics forms, petrochemical plants, mines, etc.. The Shingo Prize has become the global standard of excellence and is administered by the Shingo Institute. [6] The institute carries on Shingo’s relentless pursuit of perfection through its mission of “Improving the Process of Improvement.”
The Big Ideas for Operations Management
Shigeo Shingo foundational idea was the ‘pursuit of perfection’. Pursuing perfection meant eliminating waste of every type, such as mistakes (zero defects), lost production time due to product changeovers, and inventory. This pursuit ultimately led him to develop the pokayoke and SMED methods, as well as a single-piece flow production system. His partnership with Toyota significantly contributed to the development of the Toyota Production System (TPS) and the subsequent Lean and Six Sigma methods. His methods and ideas are more prevalent today than they were when he developed them.
Sources
[1] For a complete listing of Shingo’s books in both Japanese and English, see https://shingo.org/books/.
[2] History-biography, “Shigeo Shingo,” History-biography, 2023. https://history-biography.com/shigeo-shingo/
[3] S. Shingo and A. P. Dillon, A study of the Toyota production system: From an Industrial Engineering Viewpoint. CRC Press, 1989.
[4] S. Shingo, Zero Quality Control:: Source Inspection and the Poka-yoke System. Routledge, 2021.
[4] S. Shingo, Non-stock production: the Shingo system of continuous improvement. CRC Press, 1988.
[5] See https://shingo.org/
[6] For a list of prize recipients, see https://shingo.org/awards/